Producing exceptional design is not about reinventing the wheel, unless you’re Sophie Mallebranche. The French atelier’s expertise lies in crafting woven metal creations, taking materials that seem well known and turning them into works of art that are entirely new.
Since founding her studio in 2010, she has collaborated with the likes of Jacques Grange, interior designer to Yves Saint Laurent, and Peter Marino, hailed as “the most famous architect in fashion.” Her metal weaves adorn Chanel’s historic address on Rue Cambon in Paris, while her stainless-steel curtains hang in Alain Ducasse’s Paris restaurant at the Plaza Athénée.
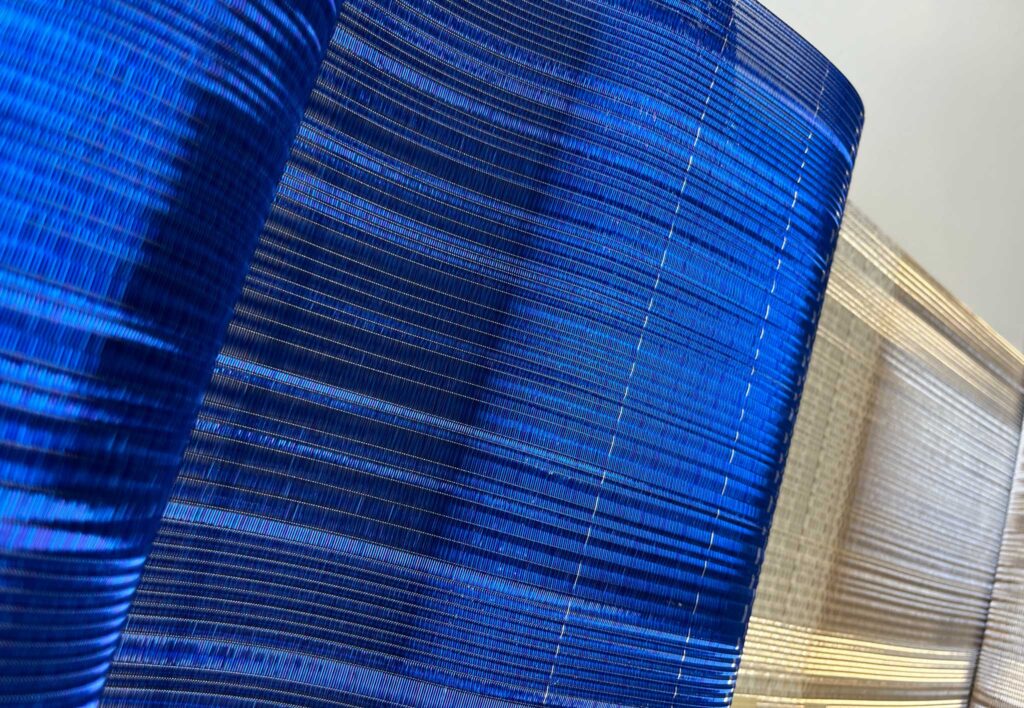
“The concept of woven metal emerged from my deep fascination with textures, metallic effects and light—elements I grew up surrounded by in my father’s chef kitchen in Normandy,” she says. “This environment shaped my vision, which drew inspiration from traditional textile techniques I learned at Duperré Higher School of Applied Arts. By adapting these techniques to metal, I created a new material language that seamlessly bridges art and architecture.”
Mallebranche has worked on more than 40 yacht projects, including the 400-foot (122-meter) Lürssen Kismet and the 361-foot (110-meter) Oceanco Kaos. Each piece is made to order with a range of uses, including wall coverings, wall panels, doors, cabinet fronts and works of art. Glass laminated panels serve as space dividers in dining areas and spas, and are visually arresting when mounted on a yacht’s staircase or elevator shaft. “Our materials are highly sought after in the industry, not just for their elegance, but for their resilience in marine environments,” she says.
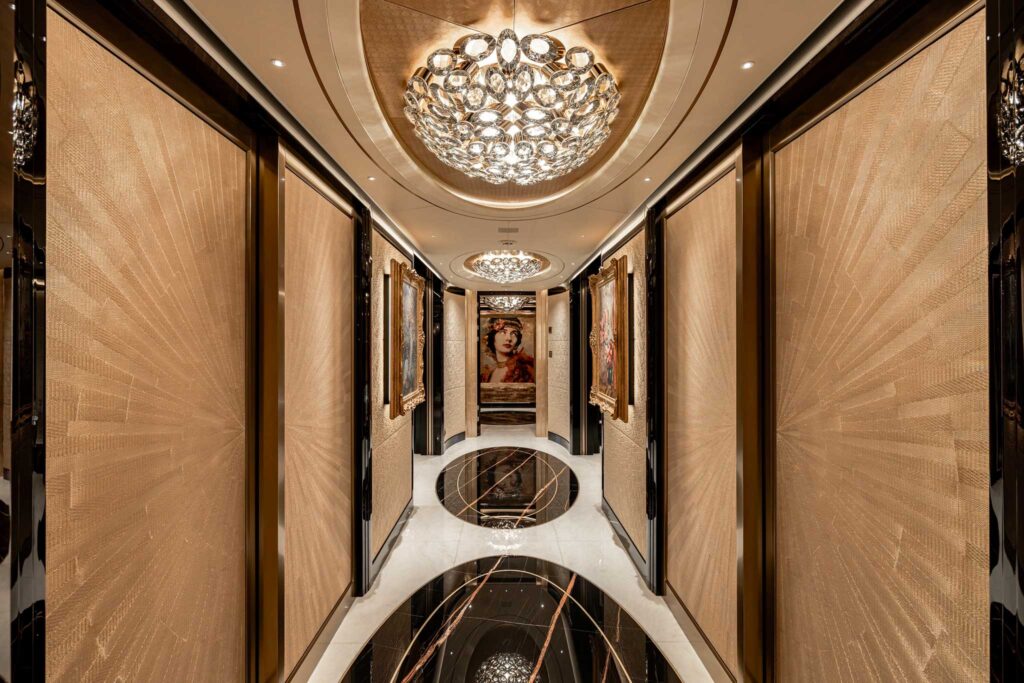
She developed her woven-metal processes at a dedicated mill in the Loire Valley, blending advanced techniques with artisanal expertise. The finest metallic wires, including 316L stainless steel strands, are interwoven with
silver-plated enameled copper to produce a bespoke material. The stainless steel provides durability and stability, while the copper adds color and texture.
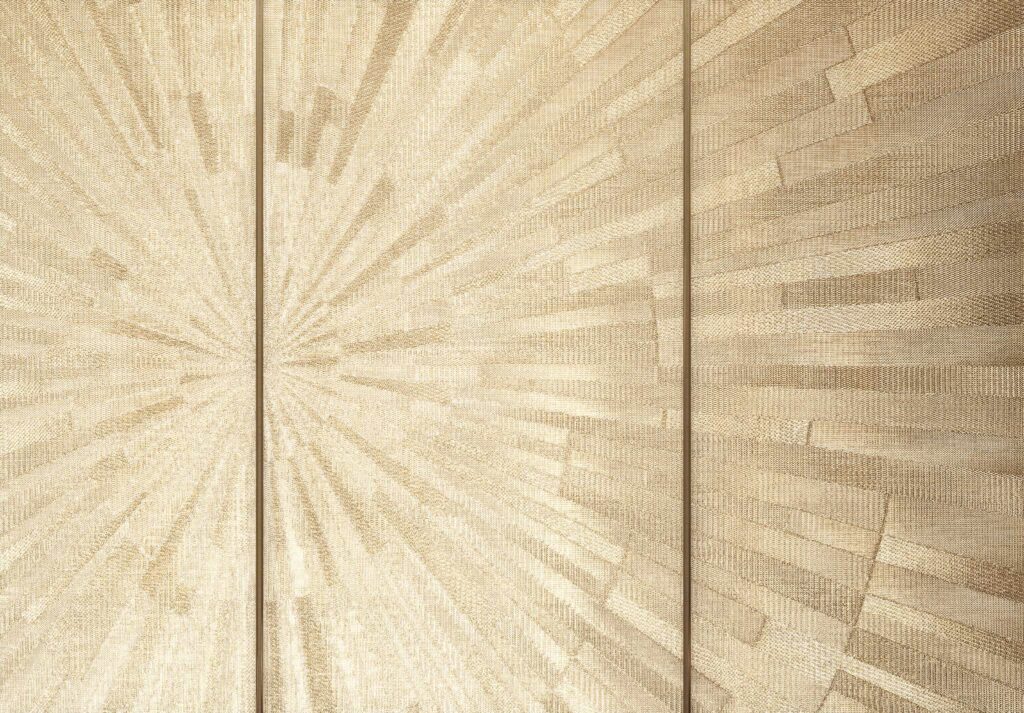
“The process requires precision, as each material behaves differently,” she says. “Stainless steel’s resilience contrasts with the delicate nature of the enameled copper, demanding careful handling to achieve flawless results.”
Aboard Kismet, she created a series of diptychs and quadriptychs, developed in collaboration with the Reymond Langton design firm and culminating in the creation of showstopping doors. Each door panel is custom made and adorned with Mallebranche’s “grand soleil” motif, an elaborate sunburst pattern that became a central feature of the yacht’s interior.
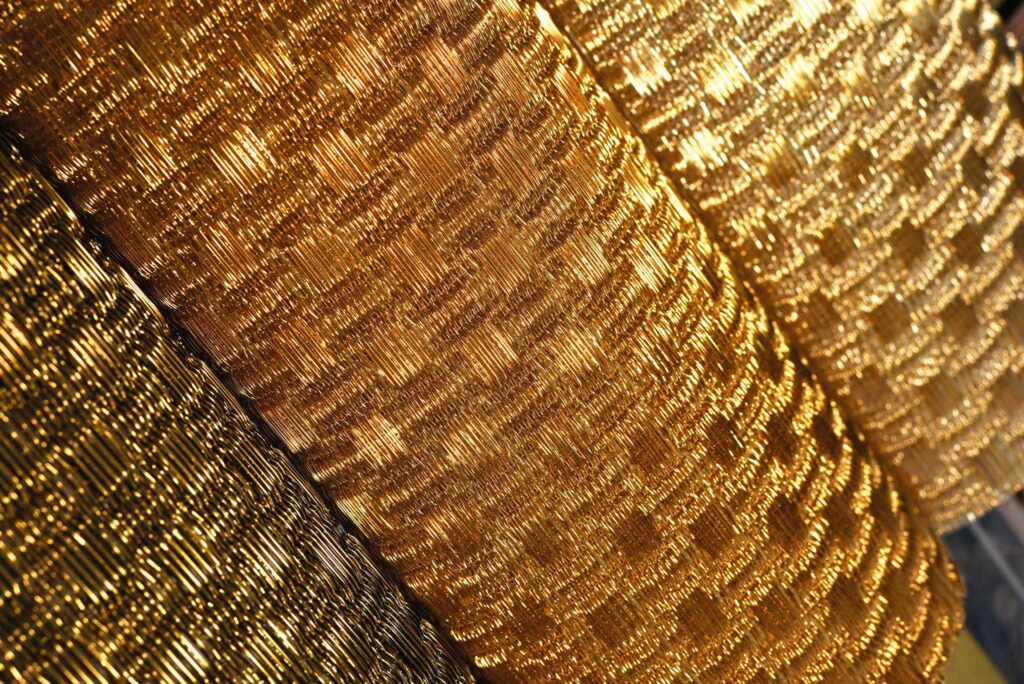
“I created 22 distinct designs that were specifically adapted to the doors’ dimensions and carefully aligned to ensure a flawless visual continuity in the owners’ suite, boudoir and bathrooms,” Mallebranche says. “It offered a refined visual division between private areas and circulation spaces.”
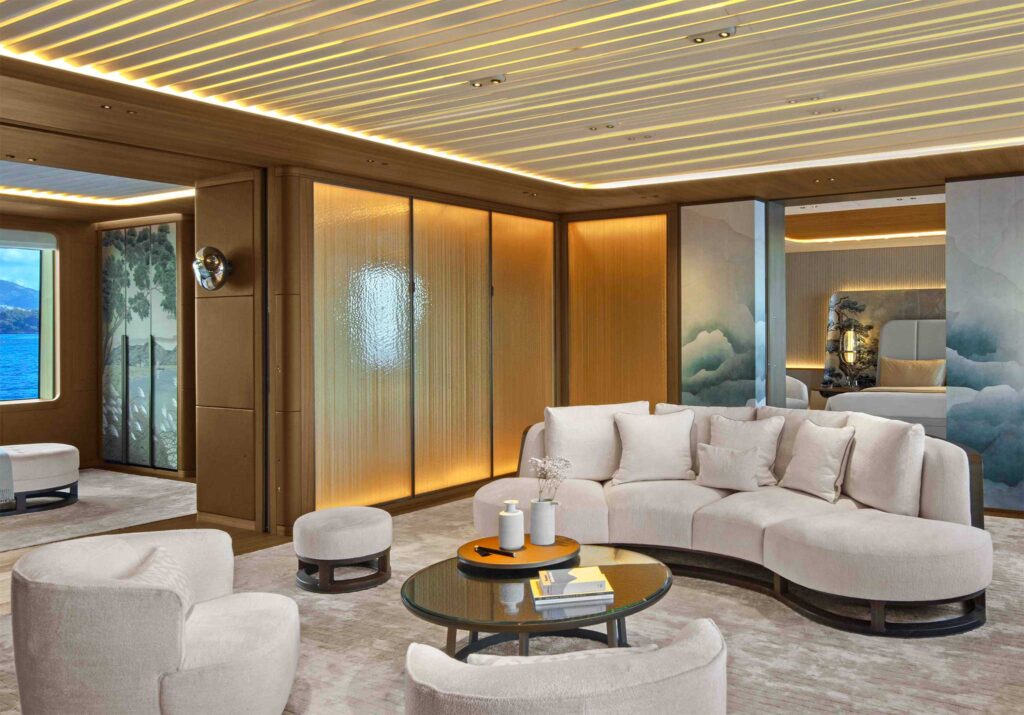
For the 345-foot (105-meter) Oceanco H3, Reymond Langton used four of Mallebranche’s woven metal materials as wall coverings in various lobbies and as glass laminated panels in the spa and owners’ suite. Aboard the 246-foot (75-meter) Admiral Kenshō, interior design studio Jouin Manku integrated a metal weave from Mallebranche’s Signature collection and laminated it in low-iron cathedral glass to create an extra layer of texture on the main salon walls. According to Mallebranche, both projects “pushed the boundaries of what woven metal can achieve by integrating seamlessly with the vessels’ luxurious yet functional designs.”
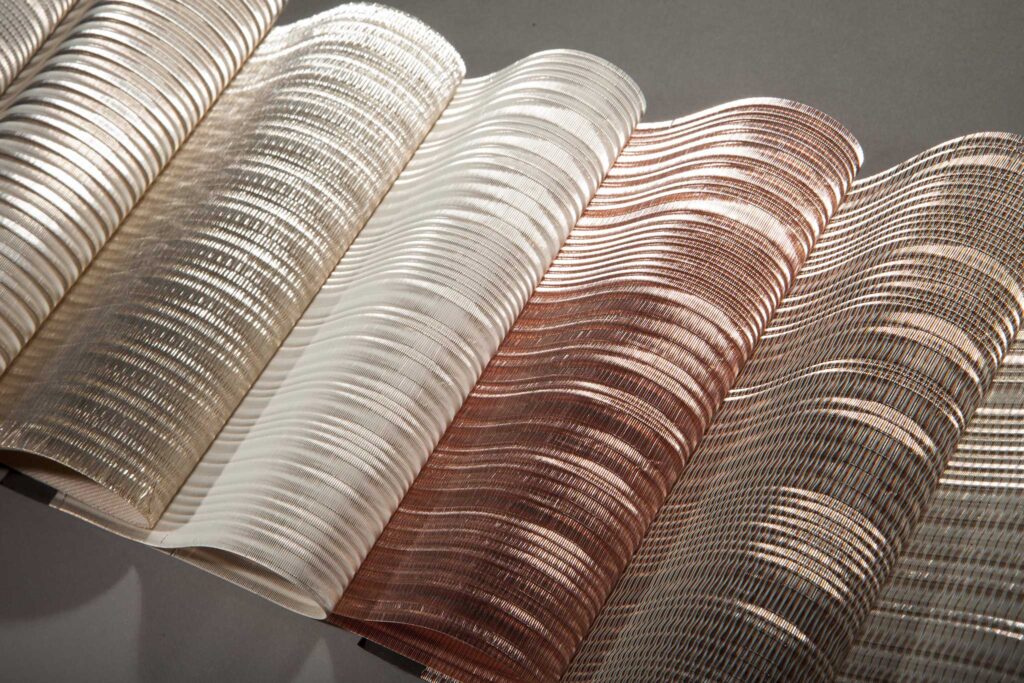
The durability and aesthetic appeal of woven metal has led to a growing demand for Mallebranche’s work among yacht designers. Its resistance to corrosion, combined with its fire-resistant finishes, make it ideal for marine environments.
Some of the more challenging requests include fine-lined images or a landscape with multiple textures in the same weave. The integration of crystals or glass beads into the weaving process is also particularly tricky. Typically, it takes eight to 12 weeks to produce one piece from design through delivery. Much of the manufacturing process is carried out by hand using advanced looms that are engineered to produce the finest quality of technical weaving. These machines are operated by artisans adept in controlling color consistency, weaving perfection and edge precision.
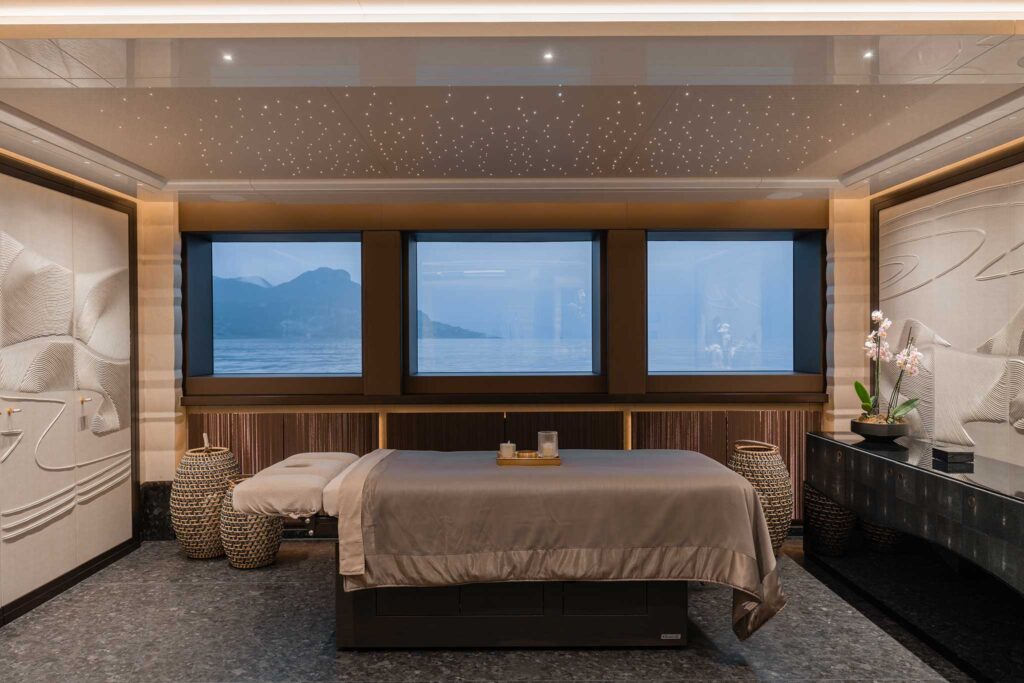
“Being able to further develop an age-old artisanal weaving technique with my innovative engineering process constantly brings my work to new heights,” says Mallebranche, who is currently developing finishes that interact with ambient light in novel ways.
In spring 2025, Mallebranche opened a “dream factory” in the Loire Valley. Its aim is to push the production processes even further, reflecting her ongoing commitment to merging technological advancement with artistic vision.
For more information: sophiemallebranche.com
Leave a comment